Quick and Reliable Product Packaging Maker Fixing Provider to Lessen Downtime
In the competitive landscape of production, the effectiveness of packaging procedures pivots on the integrity of machinery. Quick and reliable fixing services are vital in minimizing downtime, which can cause significant operational obstacles and economic losses. Recognizing the importance of prompt interventions and the function of professional professionals can transform just how businesses approach upkeep and fixings. Browsing the myriad options readily available for repair service services can be difficult. What factors should services take into consideration to ensure they are making the ideal choice for their operational requirements?
Value of Timely Fixes
Prompt repairs of product packaging equipments are crucial for maintaining operational efficiency and lessening downtime. In the busy setting of manufacturing and product packaging, even minor malfunctions can cause considerable delays and performance losses. Addressing problems quickly makes sure that equipments operate at their ideal capability, thus guarding the circulation of procedures.
Moreover, regular and prompt upkeep can protect against the escalation of minor problems into significant malfunctions, which commonly incur higher repair prices and longer downtimes. A positive method to machine fixing not just maintains the stability of the equipment yet likewise boosts the general dependability of the production line.
Additionally, prompt repair work add to the durability of product packaging machinery. Equipments that are serviced immediately are less most likely to struggle with extreme wear and tear, enabling companies to optimize their investments. This is specifically essential in sectors where high-speed packaging is crucial, as the demand for constant efficiency is critical.
Advantages of Reliable Company
Reputable solution companies play a crucial duty in making certain the smooth procedure of product packaging machines. Their proficiency not just boosts the performance of fixings yet additionally adds dramatically to the long life of tools.

In addition, a respectable provider uses thorough assistance, consisting of training and advice for team on equipment procedure and upkeep finest methods. This not just empowers staff members yet additionally grows a culture of security and efficiency within the company. Generally, the advantages of engaging dependable company expand beyond immediate repairs, favorably influencing the entire operational workflow of product packaging processes.
Typical Product Packaging Maker Problems
In the world of packaging procedures, various problems can compromise the performance and functionality of equipments (packaging machine repair). Another usual issue is imbalance, which can create jams and unequal product packaging, affecting item quality and throughput.
Electrical troubles can also interrupt product packaging operations. Faulty electrical wiring or useful reference malfunctioning sensing units may lead to erratic device actions, creating delays and enhanced functional prices. In addition, software application glitches can impede the equipment's programming, causing functional inefficiencies.
Irregular item flow is one more essential issue. This can occur from variants in product shape, weight, or size, which may impact the maker's capacity to manage things properly. Inadequate training of operators can intensify these issues, as inexperienced workers may not acknowledge early signs of malfunction or may misuse the devices.
Resolving these usual product packaging maker problems immediately is vital to preserving productivity and making sure a smooth procedure. Routine assessments and positive maintenance can dramatically alleviate these concerns, promoting a trustworthy packaging atmosphere.
Tips for Minimizing Downtime
To minimize downtime in product packaging procedures, executing a proactive upkeep method is important. On a regular basis arranged maintenance checks can recognize prospective issues prior to they intensify, ensuring makers operate successfully. Developing a routine that consists of lubrication, calibration, and evaluation of essential parts can considerably lower the frequency of unanticipated malfunctions.
Training personnel to run machinery appropriately and acknowledge very early warning indicators of malfunction can additionally play an important role. Encouraging operators with the expertise to carry out standard troubleshooting can avoid small issues from creating major hold-ups. Preserving an efficient inventory of vital extra components can expedite repair services, as waiting for components can lead to extensive downtime.
Additionally, recording device efficiency and upkeep tasks can help recognize patterns and persistent problems, permitting targeted treatments. Integrating innovative tracking technologies can offer real-time data, allowing predictive upkeep and lessening the threat of abrupt failings.
Last but not least, cultivating open interaction in between drivers and upkeep groups makes certain that any irregularities are quickly reported and resolved. By taking these positive procedures, organizations can boost functional effectiveness and significantly minimize downtime in product packaging processes.
Selecting the Right Repair Service Service
Selecting the ideal repair work service for packaging equipments is an important choice that can considerably influence operational performance. A well-chosen provider makes certain that your machinery is repaired quickly, successfully, and to the greatest standards. Begin by evaluating the service provider's experience with your certain kind of product packaging equipment. A specialist acquainted with your equipment can diagnose concerns much more accurately and execute options a lot more rapidly.
Following, consider the service company's credibility. Seeking feedback from other services within your market can offer insights into dependability and quality. Accreditations and collaborations with acknowledged equipment suppliers can additionally show a commitment to quality.
In addition, assess their action time and accessibility. A company who can offer punctual assistance reduces downtime this website and maintains manufacturing circulation constant. It's also crucial to inquire concerning guarantee and service guarantees, which can show the self-confidence the supplier has in their job.
Final Thought
Finally, the significance of reputable and quick product packaging equipment repair solutions can not be overstated, as they read this play a critical role in reducing downtime and making certain operational performance. By focusing on prompt repair work and selecting reliable company, organizations can successfully maintain and attend to typical issues performance. Applying positive upkeep methods and buying team training further boosts the durability of packaging machinery. Inevitably, a calculated method to fix solutions fosters a much more resistant manufacturing atmosphere.
Prompt repair services of product packaging devices are vital for preserving operational efficiency and decreasing downtime.In addition, prompt repairs contribute to the long life of product packaging equipment. On the whole, the benefits of engaging reliable service providers expand past immediate fixings, favorably influencing the whole functional workflow of product packaging processes.
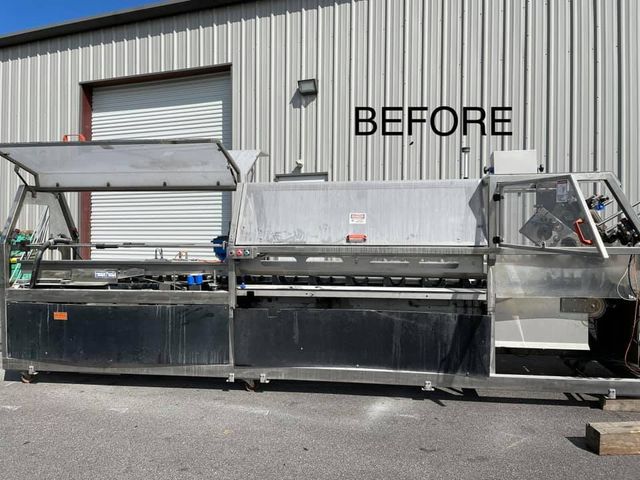